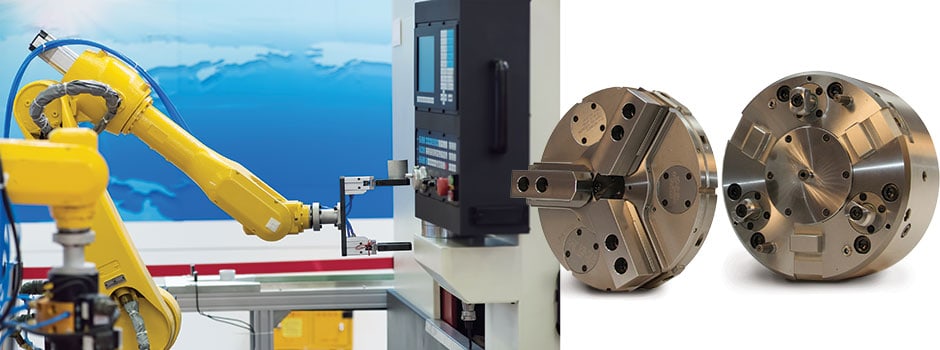
Automated Jaw Pallet System
Automated Workholding for High Mix, Low Volume Parts Machining
- Jaw Pallet replacing method allows you to change all 3 jaws at once by replacing entire Pallet
- Deliver your work-pieces and Jaw Pallets by Robot or Shuttle
- Flexible capabilities for automated robotic systems and continuous operations unattended
- Ideal for high mix, low volume production
- Precision high accuracy positioning and repeatability of pallet to chuck body
- Designed for protection from chips and contaminants
- Compact design uses less Z axis space
Watch the New Video demonstrating how the system works.
FLEX Series Robot Hand Changers
FLEX Series Parallel Jaw Grippers
Automated Jaw Pallet System
How the Kitagawa Automated Jaw Pallet System Works:
- The Promano Quick Change Capable Grippers on the Robots end of arm allows the Robot to change the rough part (loading) Grippers and finish part (un-loading) Grippers for as many different parts required to be machined.
- The Grippers also allow the Robot to change the Pallets (for the Workholding) for as many parts to be machined allowing total un-attended management of both part and Workholding handling.
- The Kitagawa Automated Jaw Pallet System Special Chuck and Cylinder can be installed on one or both Spindles allowing the Jaw Pallets for the rough and finish part geometries to be changed.
- The Robot loads the Pallet Gripper and inserts the Jaw Pallet into the chuck body where it is locked into place and ready for an internal or external gripping of the part.These Jaw Pallets are designed to maintain very close tolerance between changes allowing high accuracy and repeatability of both locating and gripping geometries.
- The Pallets are Equipped with Special Jaws and Dust covers designed to prevent any contaminants from intrusion and can be supplied with part specific engineered workholding solutions.
- The Robot then changes its Kitagawa Promano Gripper to the first part geometry to be loaded and machined.
- As the robot loads the first part to be machined the Kitagawa Automated Jaw Pallet grips it securely and accurately.
- As the machining process starts the Robot then proceeds to change the Kitagawa Promano Quick Change capable Gripper to the finish geometry.
- In this instance no change needed as both Grippers required for loading and un-loading the part or parts are on one end of Robot arm Bracket.
- As the Robot loads the next part to be machined it confirms the presence of the finished part and un-loads the finish part allowing the process to continue for any quantities needed.
- During the machining process the Robot continues with other tasks like inspection, part washing etcetera, both Machining and changing of the work handling happen internal of each other’s cycle time.
- When the desired number of parts needed to be machined is reached and the final part is un-loaded the Robot then changes its Promano Gripper to accommodate the Kitagawa Automated Jaw Pallets.
- The Robot then proceeds to equip the machine tool with the Workholding needed to machine the next group of completely different parts, in any quantity.
- The Robot then changes its Promano Gripper to the next completely different part geometry to be machined and the process is repeated all over again.
This automatic jaw change chuck is ideal for high mix low volume production and use with automated robot load.
Features
- Face plate equipped with air seating confirmation as standard option
- Face plate locator achieves high precision repeatability
- Z axis stroke range extended due to smaller chuck body
- Lighter body prevents wear and tear on spindle
- Change three jaws quickly and easily by only replacing the face plate
- Use with automated robot load – allows unattended operation overnight
Specifications
Size | inch | 10 |
Max. Speed | min-1 | 3500 |
Jaw stroke for Main clamp | mm | 9.0 |
Plunger Stroke | mm | 20.0 |
Max static gripping force | kN | 81 |
Max. input | kN | 37.5 |
Mass of Faceplate | kg | 18 |
Mass (including Faceplate) | kg | 66 |
Inertia (including Faceplate) | kg/m2 | 0.6 |
Thickness of chuck | mm | 170 |
Stroke for clamping Faceplate | mm | 22 |
Clamp force for Faceplate | kN | 45 |
Gripping diameter | mm | 54~254 |
Matching Cylinder | YG385W19C |