We have a full service shop in our facility to offer our customer’s Kitagawa brand factory certified repair work – the ONLY certified repair center for Kitagawa brand chucks in the US. The process starts with the disassembly of the chuck or cylinder for full cleaning and inspection. After inspection the customer is consulted to determine the best course of action, repair or replace. If repair is determined to be the best course of action, the repair will be completed using only Kitagawa original parts. After the repair is complete the chuck or cylinder is mounted to a test stand for functionality and accuracy testing. Cylinders undergo full pressure testing, along with our standard functionality tests, to ensure that what we send out is properly repaired.
NEW! We also offer comprehensive on-site repair services to meet the needs of machine shops requiring minimal down-time for repairs. Our service allows operations to save time and money on shipping damaged components to a repair center, which can cost operations thousands of dollars in lost revenue. We will dispatch expert technicians to your facility to analyze the workholding and provide an immediate, in-person diagnosis of the problem. Service time is cut drastically and can be completed within one day, depending on the difficulty of the restoration. During the evaluation and repair, our technicians will educate operators on preventative maintenance processes.
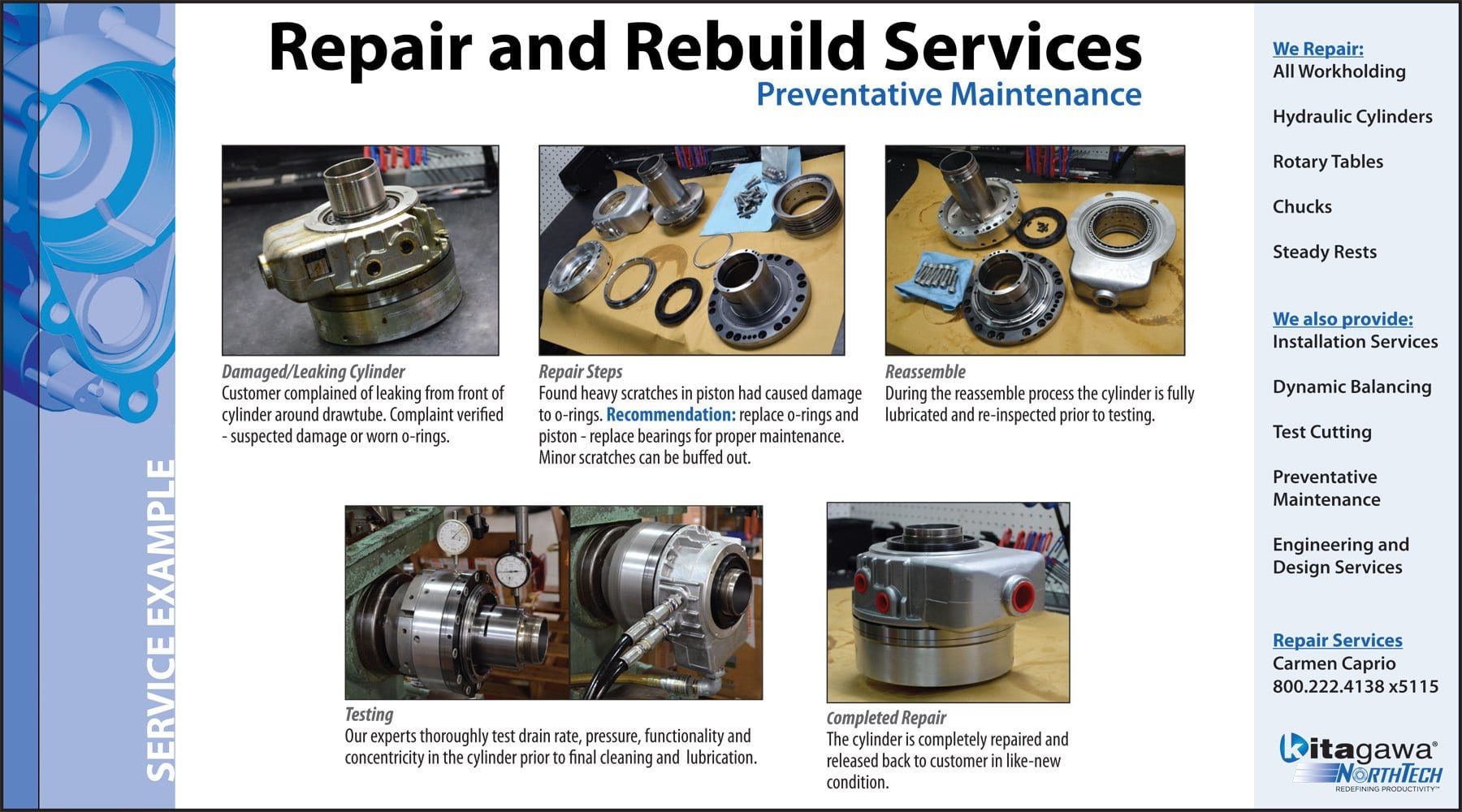